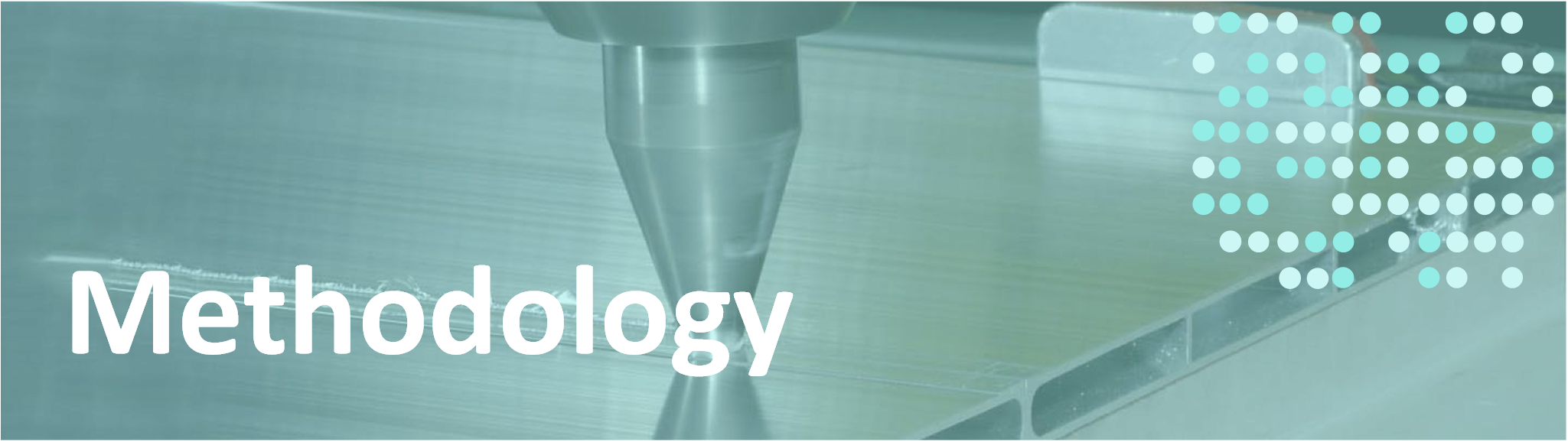
STWIN aims to eliminate defects in the welding process by exploiting the specific advantages of the friction stir welding process in combination with real-time quality control and AI
STWIN pursues to join plain carbon and high strength steels, dissimilar materials and dissimilar thicknesses by friction stir welding. To achieve this aim, the project work will be carried out in the following phases:
- Real time quality monitoring for friction stir welding
Within STWIN, a novel real time monitoring system will be built and demonstrated. The intention is to use the measured process parameters like rotation speed, forces, etc., complemented with other measurements, extracted from a smart combination of sensors.
- Development of Artificial Intelligence models and Digital Twin
The basic of a digital twin is to create a digital counterpart of the reality and linking physical and digital objects in an accurate manner. STWIN will focus on real time monitoring of FSW with the help of a digital twin and AI Machine Learning models.
- Manufacturing processes optimisation
In STWIN, tools will be tested and further improved for welding of steel. Under this context, new tool geometries will be explored in order to optimise the joint properties and tool life.
- Demonstration and validation
In order to validate the developed methods and optimisation strategies at industrial level, STWIN will have a strong demonstration component, comprising the implementation of 3 case-studies. Specifically, the following: joining of high-strength steels for crane applications, welding of complex geometry and mixed materials for automotive sector and joining of aluminium to steel for trailer applications.